What’s Hiding Your Quality Issues? 3 Causes of Poor QC Visibility in Manufacturing
17/Apr/2025
What’s Hiding Your Quality Issues? 3 Causes of Poor QC Visibility in Manufacturing
Yet, many manufacturers still struggle with poor quality control visibility, and the consequences can be costly. Without real-time insight into when and where defects occur, issues often go unnoticed until they reach the final inspection. This lack of visibility can lead to missed defects, inconsistent product quality, and delays in identifying root causes. Entire batches may be scrapped or recalled simply because it's unclear which products were affected.
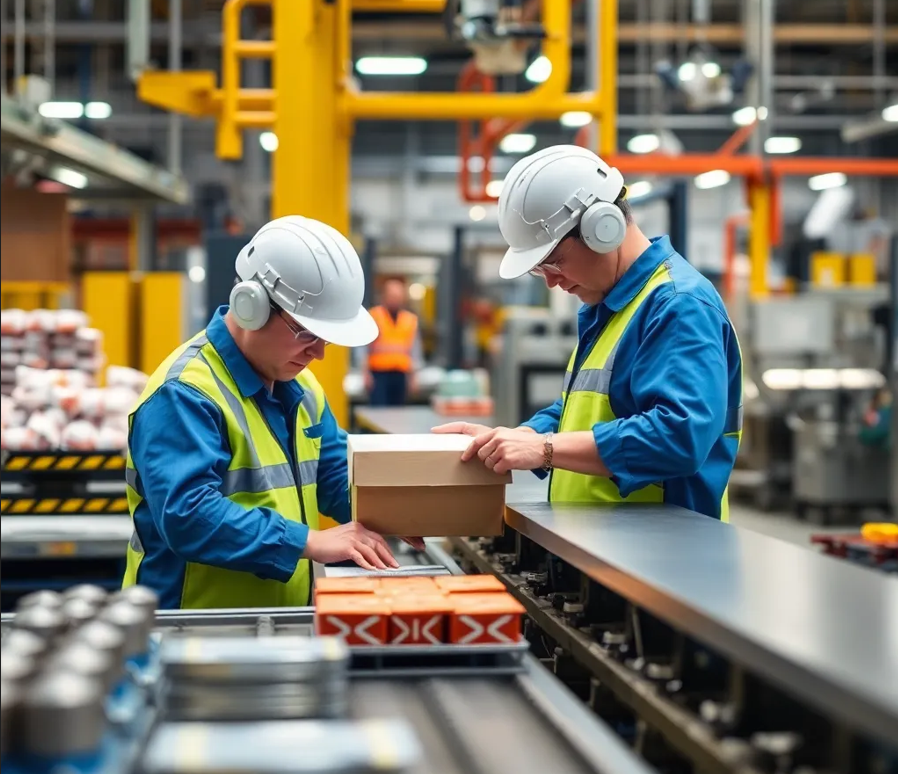
The result? The quality teams are left sifting through incomplete paper logs, and managers are stuck making decisions with outdated or inaccurate data. Poor QC visibility doesn’t just affect product quality but it slows down the entire production chain and threatens customer satisfaction.
Difficulty Tracing Defective Batches Across the Production Line
One of the most common problems in manufacturing is when a defect is found but no one knows exactly where it came from. Let’s say a customer reports a faulty product, or a defect is caught during final inspection. The next step should be simple: trace it back to the batch, identify when and where it was made, and fix the issue. But without proper traceability, this becomes a guessing game. The core problem? There’s no real-time tracking system that links each product or batch to its full production history.
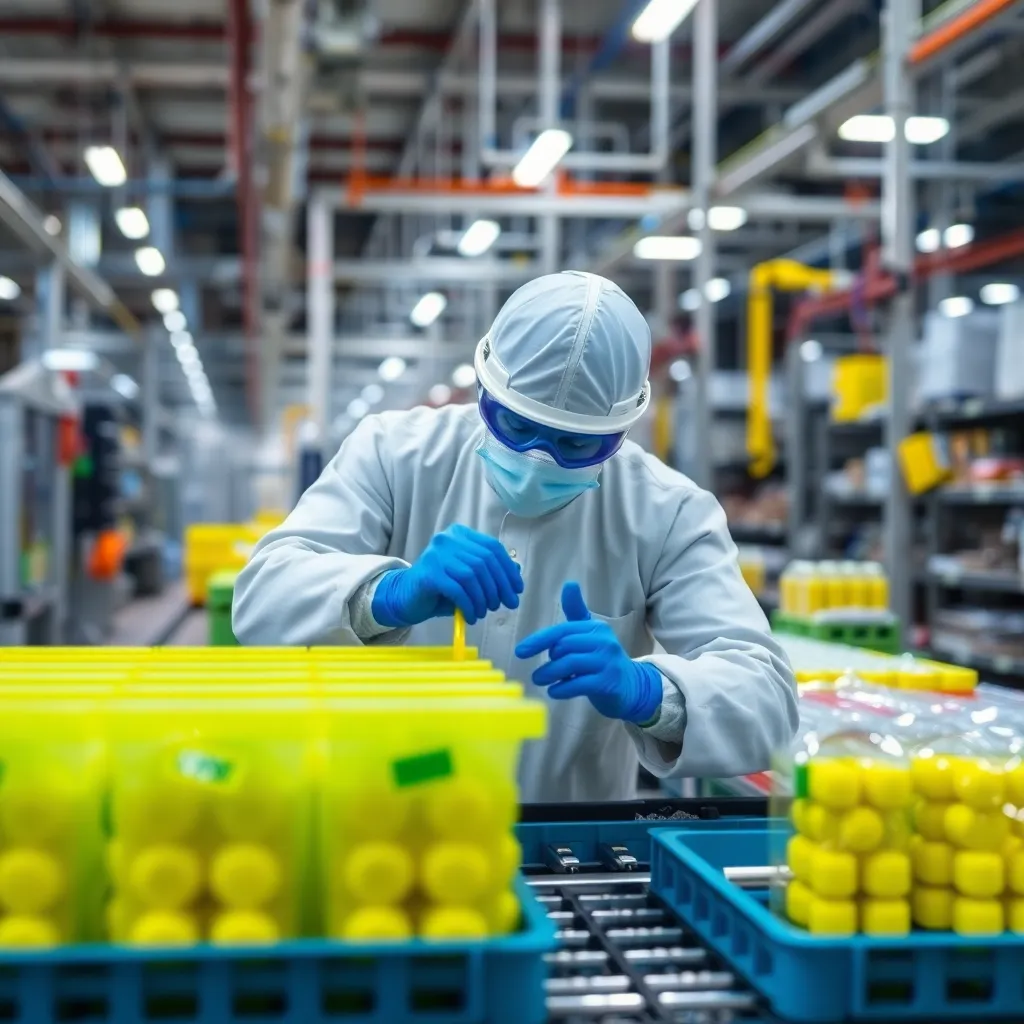
Manual Quality Checks Cause Inconsistent Data Collection
In many factories, quality control is still done the old-fashioned way with pen, paper, or basic spreadsheets. Operators perform checks on parts or products, then write down results by hand or input them into a computer later. While this might seem fine on the surface, it opens the door to a lot of problems.
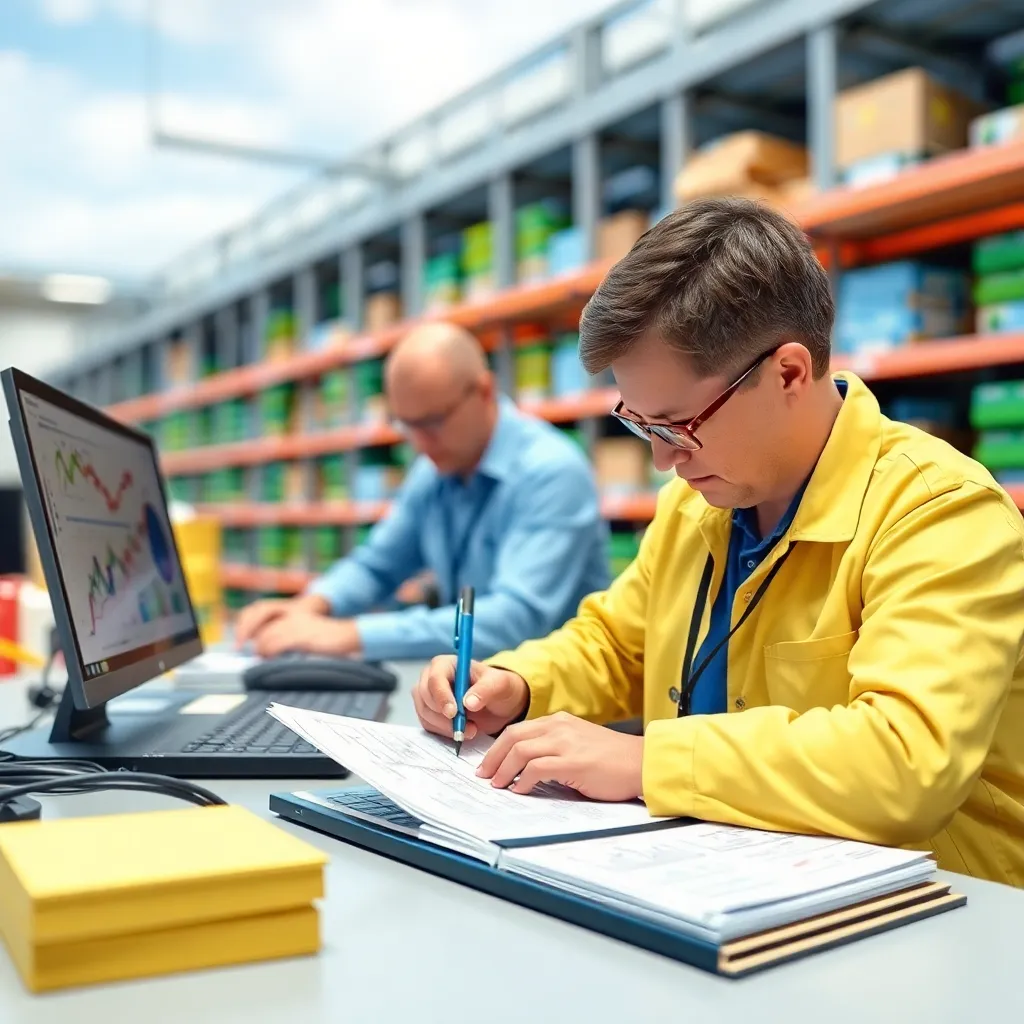
Here’s what often happens: - Data is missing because someone forgot to record it.
- Handwriting is unclear, or numbers are recorded incorrectly.
- Different operators record things in different ways, making it hard to compare or analyze.
- QC logs may be misplaced, or updates are delayed because they're stored physically or entered manually hours later.
The real problem? There’s no standardized, digital system in place to collect and store quality check data accurately and in real time.
Lack of Real-Time Quality Insights
In many manufacturing operations, quality issues are only discovered after the damage is done. Why? Because quality data is often trapped in siloed systems, on paper forms, or entered manually at the end of a shift.
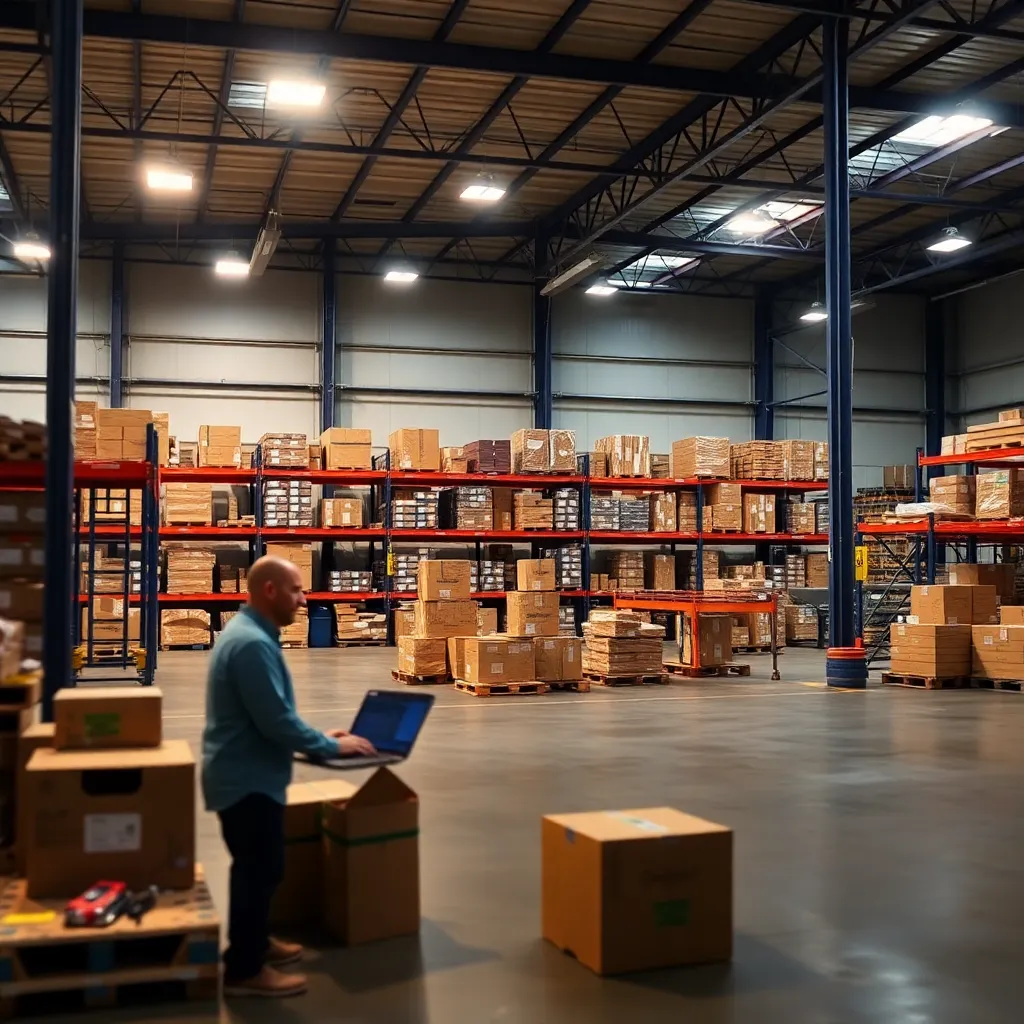
Here’s how this pain point shows up in real life: - A production line is turning out defective parts for hours before anyone notices.
- QC data is collected manually, then updated into a system at the end of the day, delaying important decisions.
- Managers don’t have a live dashboard or alerts, so they can’t react to trends like increasing defect rates or failed checks in real time.
More defective products, wasted materials, longer downtimes, and delayed responses. Opportunities to fix problems early are missed because the information isn’t flowing fast enough.
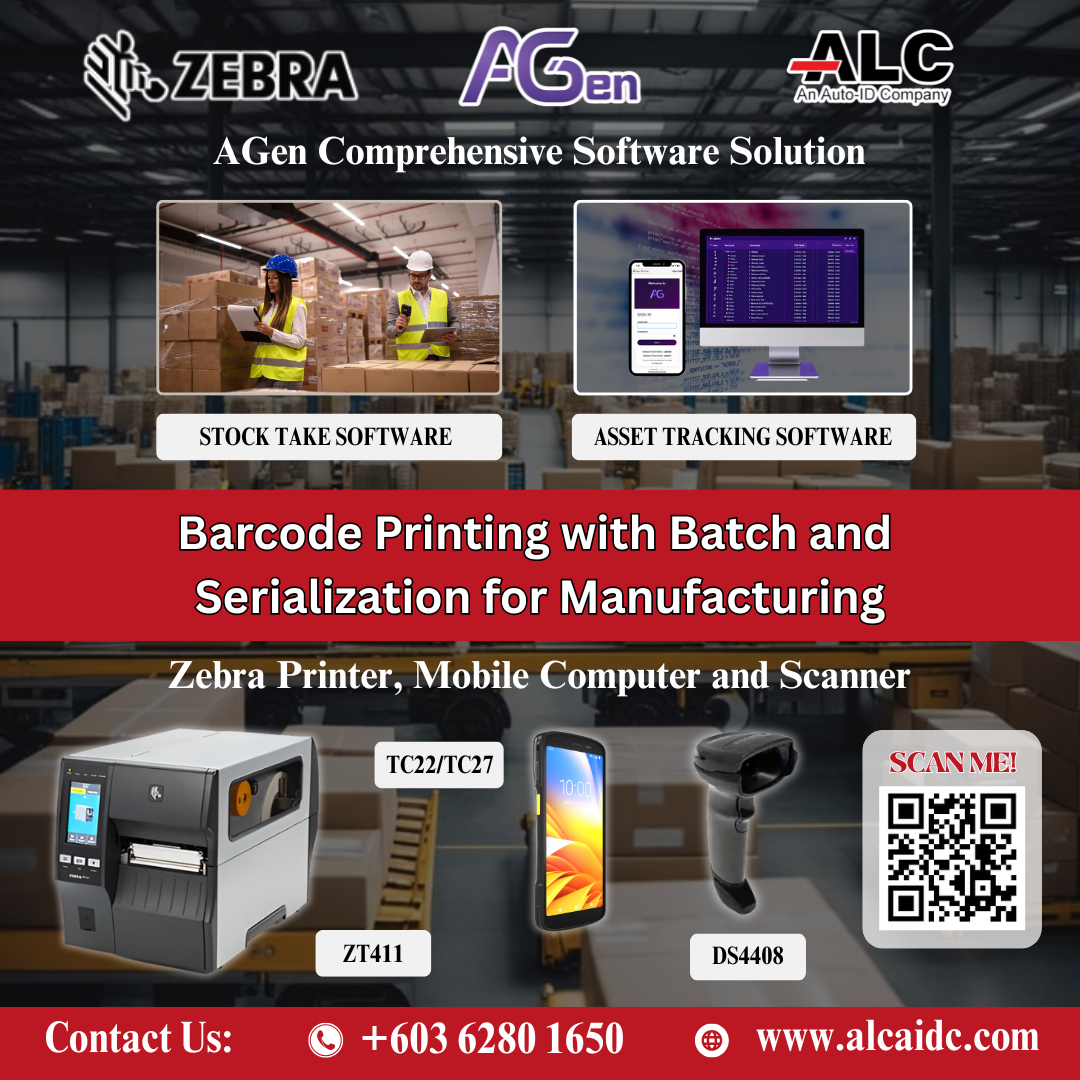
Solution to these 3 Major Problems
With AGen Software and Zebra devices working together, manufacturers can finally see what’s happening on the production floor clearly and in real time. AGen Software brings automation, traceability, and visibility to your production line which is turning manual processes into smart workflows that save time, reduce errors, and improve product quality.The Zebra ZT411 printer creates serialized barcode labels at every stage, while operators use the Zebra TC22/TC27 mobile computers and DS4408 scanners to scan items and enter quality check results.
Everything is tracked and stored automatically, so there’s no more messy paperwork or guessing. If a defect happens, the AGen system shows exactly which batch is affected, making it faster and easier to fix problems before they grow. This setup helps teams work smarter, catch issues early, and deliver better quality products with less waste.
Are you ready to improve the way your operations run? Scan now or contact us immediately to get your FREE DEMO today!
by:
stephanie
|