28 Common Reasons Why Factories Perform Relabeling in Warehouses and Production Lines.
16/Apr/2025
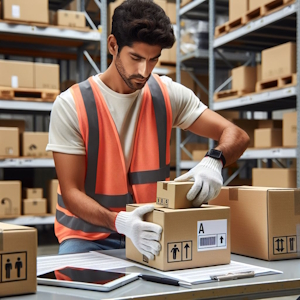 Introduction Relabeling is a critical process in many factories and warehouses, ensuring products meet regulatory, operational, and customer-specific requirements. From correcting errors to adapting to market demands, relabeling helps maintain accuracy, compliance, and efficiency across the supply chain. In this article, AGen explains to you 28 common reasons why manufacturers and logistics teams routinely perform relabeling in their operations.
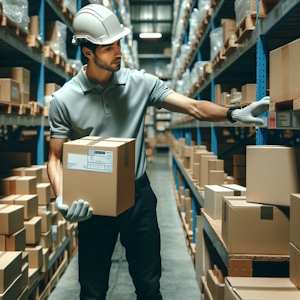 1. Batch Tracking: For better traceability, especially in industries like pharmaceuticals and food, products might need new labels to include batch numbers or production dates.
2. Customer Feedback: Based on customer feedback, products might need updated labels to address concerns or improve clarity.
3. Customer-Specific Labels: Some customers may require specific labeling for their orders, which necessitates relabeling to meet these unique demands.
4. Customs Requirements: Products being shipped internationally may need new labels to meet specific customs requirements or to include additional documentation.
5. Correcting Errors: If there were errors in the original labeling, such as incorrect information or barcodes, relabeling is required to correct these mistakes.
6. Damaged Labels: If labels are damaged, smudged, or otherwise unreadable, they need to be replaced to ensure accurate identification and tracking.
7. Damage During Transit: If labels are damaged during transit to the warehouse, they need to be replaced to maintain accurate tracking and identification.
8. E-commerce Requirements: With the rise of e-commerce, products may need new labels to meet specific online retail requirements, such as additional barcodes or QR codes for tracking.
9. Environmental Labels: Products might need updated labels to reflect new environmental certifications or sustainability information.
10. Expiration Date Updates: For products with extended shelf lives or updated expiration dates, relabeling ensures that the correct information is displayed.
11. Inventory Management: When inventory systems are updated or changed, relabeling ensures that all products are correctly tracked and managed.
12. Language Requirements: Labels may need to be updated to include translations or additional languages for different markets.
13. Marketing Campaigns: Special marketing campaigns or limited time offers might require new labels to attract customer attention and communicate the promotion effectively
14. Product Bundling: When products are bundled together for special offers or promotions, new labels are needed to reflect the combined package details.
15. Product Recalls: If a product is recalled due to safety concerns or defects, it may need to be replaced with updated information or warnings before being redistributed.
16. Product Updates: If there are changes in product specifications, ingredients, or features, new labels are required to reflect these updates.
17. Regulatory Compliance: Sometimes, products need new labels to comply with updated regulations or standards.
18. Rebranding: Companies may update labels to reflect new branding or marketing strategies.
19. Returned Goods: Products returned to the warehouse might need new labels if the original ones are damaged or if the product needs to be repackaged.
20. Seasonal Promotions: Products might need new labels to reflect seasonal promotions or special offers.
21. Seasonal Adjustments: Products might need relabeling to reflect seasonal changes, such as different storage conditions or handling instructions during different times of the year
22. Serialization Tracking: For better traceability, especially in industries like electronic, electrical, pharmaceuticals and food, products might need new labels to include serial numbers or production dates.
23. Special Handling Instructions: Products requiring special handling or storage conditions might need new labels to clearly communicate these requirements
24. Supplier Changes: When there is a change in suppliers, products might need new labels to reflect the new source or to meet different supplier requirements.
25. Technology Upgrades: Implementing new technologies, such as RFID tags or advanced barcoding systems, may require relabeling to integrate these new features.
26. Quality Control: Relabeling can be part of quality control processes to ensure that all products meet the required standards before they are shipped out.
27. Quantity Change: Relabeling can be part of quantity change processes to ensure that all products meet the quantity requested by customers before they are shipped out.
28. Warehouse Reconfiguration: If the warehouse layout is changed or optimized, relabeling might be necessary to ensure that all products are correctly identified and located within the new setup.
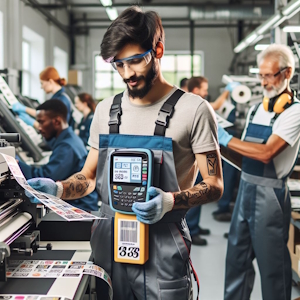
Summaries Relabeling is more than just a corrective action—it's a vital part of maintaining product integrity, meeting customer expectations, and ensuring regulatory compliance. Whether due to labeling errors, language updates, branding changes, or logistical needs, factories rely on relabeling to stay agile and efficient. Understanding these 28 common reasons can help businesses improve their labeling strategies and minimize disruptions across the production and supply chain.
by:
pang
|