Mastering Warehouse Digitization: 13 Practical Guide for First-Time Users
11/Jan/2024
To achieve a seamless inventory control process flow, clear collaboration between project managers and warehouse managers is crucial. By following these logical steps, your warehouse team can optimize operations and maintain smooth daily workflows. Remember, this process solution is designed for the entire team, not just individual users.
Standardized Operating Procedures (SOPs) should be established and agreed upon during the process flow design to ensure consistency and efficiency in warehouse operations. These SOPs will serve as valuable guidelines for your team.
Discover the Roadmap for Success: Collaboratively Implementing a Digital Inventory System with Project Managers.
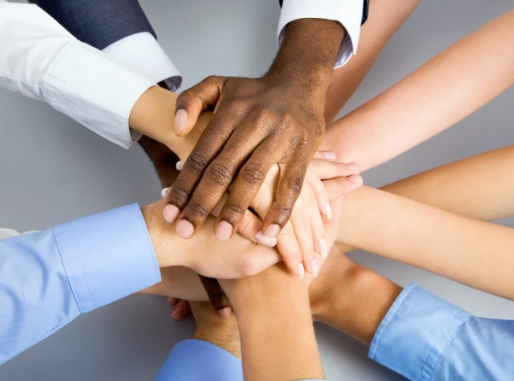 Step 1: Securing Team Commitment
The warehouse manager's enthusiasm for and strong commitment to transitioning to a digital inventory system is crucial for success. This system offers improved accuracy, efficiency, and real-time data insights, building on decades of proven success worldwide. To ensure a smooth transition, we recommend scheduling initial team meetings and providing training resources to address any concerns and build confidence. This is an ongoing process as we work together to unlock the full potential of digitalization.
Estimation: 1 day
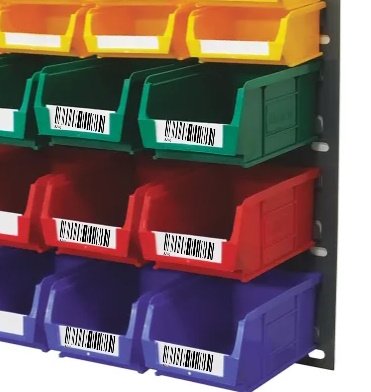 Step 2 - Location labeling.
To kickstart the process, you'll receive a label printer, labels, and ribbon from the project manager. Downloaded with dedicated printing app, connect to the printer via Bluetooth, and your labels will be printed directly on your phone. No bulky complicated software needed! Mobile phone printing offers increased flexibility, convenience, and real-time solution, enabling you to label on the go and adapt to changing inventory needs. With clear and organized location labels, you'll be well on your way to efficient warehouse management and accurate inventory tracking.
Estimation 3 days
Step 3 – Location Label checking.
To ensure flawless scanning of location barcodes, run the mobile phone's apk application (provided by the project manager) and test printed location stickers for readability.
Estimation 2 days
Step 4 – Location Label placement. For optimal efficiency and scan accuracy, prioritize a consistent approach to location sticker placement. Avoid relying on personal preferences and instead, implement a standardized system based on operational considerations.
Estimation 2 days
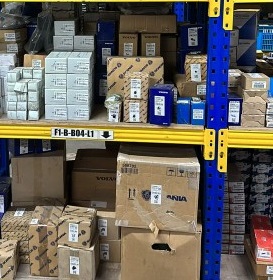 Step 5 – Object Label Printing: Streamlined Mobile Process The project manager will set up your mobile phone printing with QRCode labels, ribbons, and the necessary software (AGen). You'll access it via a downloaded URL or APK directly on your mobile device. This mobile-based printing streamlines object label creation. Simply download the app, connect to the printer via Bluetooth, and print your labels directly on your phone. No bulky desktop or complex software needed!
Estimation 3 days
Step 6 – Verify Object Label Scan ability for Optimal Inventory Control
To ensure your object labels are scanned flawlessly and contribute to accurate inventory management, perform a quick mobile barcode verification test with the APK application provided by the project manager. Use the same app onto your mobile phone and scan the barcodes on your newly printed labels.
Estimation 2 days.
Step 7 – Object Label sticking. For accurate inventory tracking, adhere to the one-sticker-one-object principle. Apply the printed label directly to each individual item you wish to track. Inventory control solution isn't designed to track multiple items within a single carton box; each sticker represents a unique identity. Therefore, if a large carton contains 12 small objects you want to track, please print and apply 12 separate labels, one for each item.
Estimation 2 days
Step 8 – Exception handling. While trying to save costs, some warehouse managers suggested using one sticker for an entire carton box with multiple items inside. This approach might seem efficient, but it can actually lead to confusion and mistakes for your workers during their daily tasks. These mistakes could cost you time and money in the long run, making this type of "saving" counterproductive.
We understand the desire to be cost-conscious, and if you still prefer this approach, we can accommodate it. However, please be aware that this may increase the chance of errors in your inventory tracking by up to 5%. For example, with RM100 million worth of goods, this could lead to losses of up to RM5 million.
It's important to weigh the potential risks and costs before making a decision. We recommend using individual stickers for each item to ensure smooth operations and accurate inventory tracking, ultimately saving you time and money in the long run.
Estimation 10 days
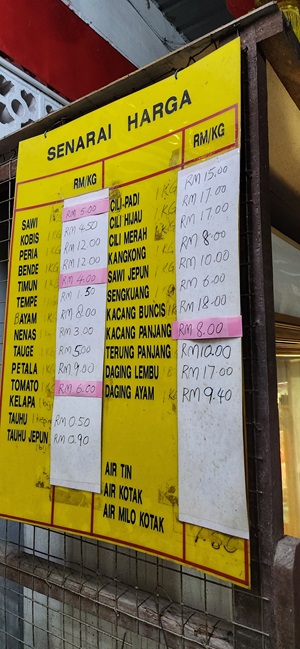 Step 9 – Object receiving. Once your barcoded objects arrive, the project manager guides you through digital receiving. Choose the supplier, scan the carton barcode, and select the bin location - AGen automatically sends your data to the server, completing the process and providing real-time inventory tracking.
Estimation 3 days.
Step 10 – Receiving reporting.
Daily, review AGen's receiving report to ensure physical deliveries match digital records. This accuracy is your 100% responsibility, Warehouse Manager. Immediately report any discrepancies between physical stock and digital values to minimize errors and safeguard inventory control. Remember, proactive reconciliation drives efficient operations and protects your valuable assets.
Estimation 2 day.
Step 11 – Item Delivery. Before outgoing items leave the warehouse, storekeepers scan them to automatically deduct their quantity from the system. This crucial step, linked to the initial receiving process, ensures accurate inventory tracking and prevents discrepancies.
Estimation 3 day
Step 12 – Delivery reporting. AGen's daily delivery report keeps you informed. At a glance, see how many objects left the warehouse and who, specifically the storekeeper responsible, facilitated each outgoing item. This transparent system empowers you to track warehouse activity and maintain accurate inventory records.
Estimation 2 day.
Step 13 – Reviewing and improving process. To iron out any kinks in the process, the project manager and warehouse manager will collaborate online. Through open discussion, the project manager will hone the workflow based on specific needs and concerns, ensuring a smoother and more efficient experience for everyone.
Estimation 5 days
Summaries
Teamwork unlocks digital inventory success with this step-by-step guide. Label locations, objects, and track movement with mobile printing and scanning. Daily data reconciliation and reporting ensure accuracy. Collaborative fine-tuning optimizes the process for a smooth, efficient warehouse flow.
|